The retail sector, known for its dynamic and challenging settings, has witnessed a notable increase in the adoption of robotic applications in recent years. The integration of robots into various aspects of retail, both within stores and in the backend operations, holds the potential to revolutionize the entire retail industry. In this article, we’ll explore the impact of autonomous mobile robots on the retail industry and how they are revolutionizing the shopping experience.
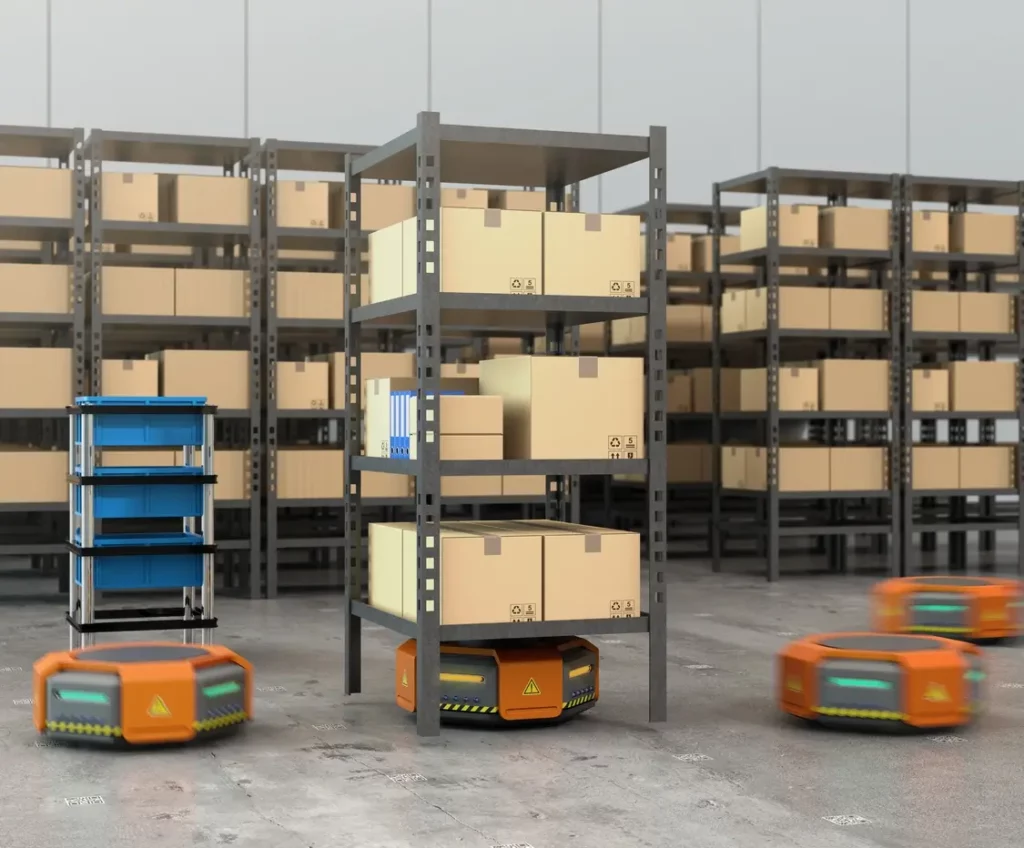
Uses of Autonomous Mobile Robots in Retail
Traditionally, retail stores were largely reliant on human labor for tasks ranging from stocking shelves to assisting customers. However, this landscape is rapidly evolving, and AMRs are now at the forefront of this transformation. Here’s how they are revolutionizing retail:
- Inventory Management: Maintaining accurate inventory levels is crucial for retailers to meet customer demand and prevent stockouts. AMRs can autonomously scan shelves, identify missing or misplaced items, and provide real-time inventory data. This allows retailers to restock shelves efficiently and reduce carrying costs.
- Order Fulfillment: In e-commerce and omnichannel retail, order fulfillment is a complex process. AMRs can be deployed in warehouses to pick, pack, and transport items to the shipping area. This automation not only speeds up the fulfillment process but also reduces errors in order preparation.
- Customer Assistance: Retailers are increasingly using AMRs to assist customers in stores. These robots can guide shoppers to specific products, answer questions, and even provide information about promotions and discounts. Some AMRs are equipped with touchscreens for interactive communication.
- Store Cleaning: Especially in the wake of the COVID-19 pandemic, maintaining a clean and hygienic store environment is essential. AMRs equipped with disinfection tools can autonomously clean and sanitize store floors, reducing the workload of human staff.
- Security and Surveillance: AMRs can enhance security in retail stores by patrolling the premises, monitoring for suspicious activities, and alerting human security personnel when necessary. They can also provide video feeds for remote surveillance.
Benefits of Autonomous Mobile Robots in Retail
The adoption of autonomous mobile robots in the retail sector offers several compelling advantages:
- Efficiency: AMRs are tireless workers that can operate 24/7, significantly increasing the efficiency of various retail operations. They can complete repetitive tasks quickly and accurately, allowing human employees to focus on more value-added activities.
- Cost Savings: While the initial investment in AMRs may be substantial, the long-term cost savings are considerable. Reduced labor costs, improved inventory management, and minimized losses due to stockouts or overstocking contribute to a healthier bottom line.
- Improved Customer Experience: By using AMRs for customer assistance, retailers can provide a more personalized shopping experience. Shoppers can get instant product information, find items quickly, and enjoy a more engaging and interactive store visit.
- Data Insights: AMRs collect vast amounts of data about store operations, customer behavior, and inventory status. Retailers can leverage this data to make informed decisions, optimize their supply chains, and tailor marketing strategies.
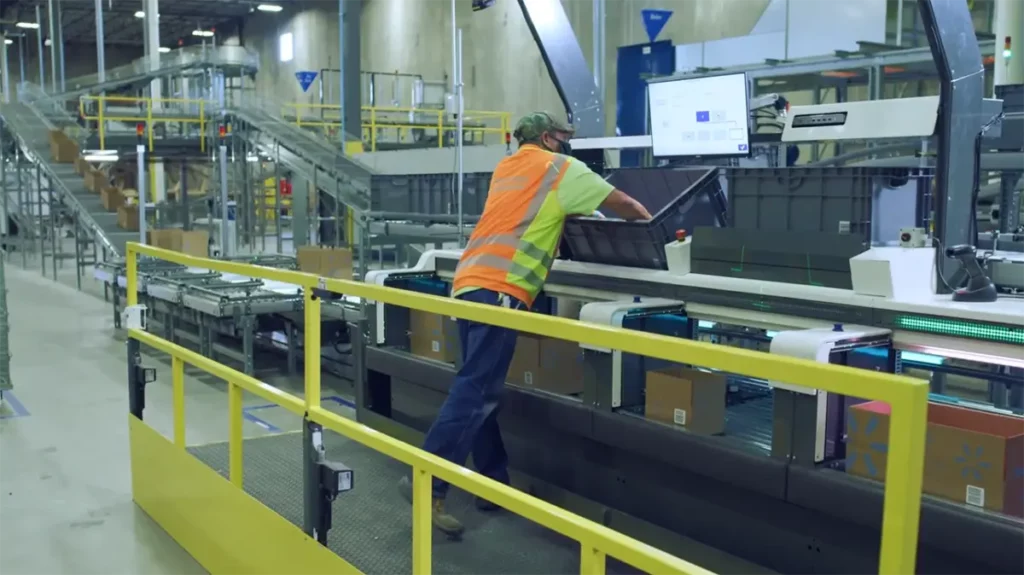
Cutting-Edge Automation at Walmart
Walmart, a global retail giant with a vast presence of 10,000 stores and 2.2 million employees in 24 countries, is strategically embracing automation to revolutionize its supply chain operations.
Walmart employs robots in 200 fulfillment centers to perform repetitive tasks swiftly and safely, significantly outpacing human capabilities. These robots automate the handling of incoming products, optimizing storage and retrieval processes. The introduction of “next-generation fulfillment centers,” exemplified by their facility in Illinois, combines human and robotic efforts with machine learning to fulfill orders with unparalleled efficiency.
At these advanced centers, merchandise undergoes a meticulously orchestrated process. Employees manually unload items, which are then routed through a conveyor belt equipped with visual recognition technology. The system directs the items to their respective locations within a vast inventory warehouse, managed by autonomous mobile robots. When an order is received, these robots retrieve items and return them to an employee at a packing station. Customized packaging, often assisted by robotic arms, ensures items are securely packed and labeled. Within as little as 30 minutes from order receipt, the package is ready for shipping.
Walmart’s commitment to automation yields substantial benefits, including reduced physical strain on employees, decreased workplace accidents, time savings, and waste reduction. Additionally, these transformations are reshaping the types of jobs offered by Walmart, with a shift towards tech-focused roles such as control technicians, quality audit analysts, and flow managers.